Conservation and restoration of lacquerware
The conservation and restoration of lacquerware addresses both the prevention and mitigation of various types of deterioration or damage to objects made with lacquer.
Production and History of Lacquer
Lacquer is a type of varnish or surface coating, which is diluted with solvent and applied in several coats to seal a substrate, hardening via a chemical reaction to create a seal.[1] There are two main categories of lacquer: Asian lacquer and European lacquer.
Asian Lacquer
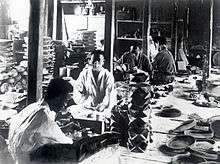
Traditional Asian lacquer has been utilized for centuries[2] and is derived from sap, prominently that from the Urushi tree; part of the sumac family grown throughout Japan, China and Korea.[3] Sap from the tree contains a chemical compound called urishol that hardens when exposed to humidity.[4] The sap is processed to remove impurities.[5] The production of lacquerware involves a process of applying a ground layer,[6] oftentimes lacquer mixed with other substances such as clay or a layer of fabric, followed by many very thin layers of processed lacquer to a substrate, typically wood, and allowing them to dry completely,[6] then curing and polishing.[2]
European Lacquer
Developed in the 17th Century, European Lacquerware, or Japanning, was influenced by the import of Asian lacquerware.[7] Japanned objects are made with a variety of shellac[8] and natural resins.[9]
Agents of Deterioration
Age
When it is produced, lacquer is a very durable substance, both waterproof and insoluble. With age, lacquer can begin to breakdown and deteriorate.[1]
Light
Lacquerware is very sensitive to exposure to light,[6] which causes photodegradation,[10] fading and discoloration.[1]
Water
Photodegraded lacquer is extremely sensitive to humidity and water. Exposure to water and other polar solvents can cause blanching, whitening of the surface from the formation of salts.[10]
Temperature
High temperatures along with moisture can cause thermochromatic change to the lacquer surface.[11]
Damage to the Substrate
The supporting structure can be damaged or lost from the effects of expanding and contracting in changing environmental conditions, including temperature and humidity, from pest damage, or deterioration from age. The damaged support may cause warping, lifting or cracking of the lacquer coating.[3]
Previous Restoration
Previous restoration such as fills and overpainting can degrade and potentially damage original surfaces over time.[12]
Conservation of Lacquerware
Preventive Conservation
Preventive Conservation measures can be used to avert damage to lacquerware caused by deterioration. Preventive methods may include limiting exposure to light to a maximum of 40 years at 100 lux or 80 years at 50 lux,[5] maintaining stable temperature and humidity levels, utilizing safe and proper art handling with gloves and proper art storage, per current professional museum standards such as those from the American Alliance of Museums.[13]
Conservation Treatment
Conservation treatment methods vary depending on the individual object and the materials used in its production.[1] Asian lacquer and European lacquer have different chemical properties, and therefore require different materials and techniques for treatment. Prior to conservation treatment, conservators and conservation scientists analyze and document the properties of the work to determine the best methods and materials for its treatment.[14] Professional conservators utilize codes of ethics for best practices, such as those from the American Institute for Conservation.[15]
Eastern and Western Techniques
Different conservation techniques are utilized to conserve Asian lacquerware in Eastern and Western cultures. Traditionally, Eastern cultures utilize Asian lacquer to repair damages and fill and consolidate losses.[3] Asian lacquer is toxic and requires training and expertise to use. The material is also not easily reversible nor readily available to attain for conservation use. Western cultures, less familiar with the techniques of producing, applying or curing lacquer, typically utilize alternate materials for conservation treatment, particularly those that can be reversed with minimal risk to the original object.[16]
Dry Cleaning
Dry cleaning is the process of removing dirt and grime from the surface of the object without the utilization of solvents. Tools utilized for dry cleaning of lacquerware can include soft brushes, microfiber cloths, cotton swabs, and fine celled absorbent sponges.[16]
Wet Cleaning
Wet cleaning is the process of further removal of dirt, grime and residue from the surface of the object that is not successfully removed by dry cleaning. Testing of various solvents should be done prior to wet cleaning the surface of the object in order to prevent possible damage to or removal of the original lacquer surface.[16] Aqueous solvents with different PH levels will have varying levels of success in the removal of dirt and grime from the surface of the lacquer, and have various levels of risk of damaging the surface. This also depends on the condition of the object prior to cleaning. Nonpolar solvents are less likely to damage surfaces that have been photodegradad.[10]
Consolidation
Consolidation is the process of stabilizing lifting and cracked areas of lacquer to minimize further damage and loss.[16] Consolidants utilized can include Asian lacquer or other synthetic or organic adhesives such as animal glue or Paraloid B-72.[16] Adhesives can be thinned with solvents in order to be wicked beneath layers of lifting lacquer or into cracks and allowed to dry while securing the loose area in place.
Filling Losses
Different types of fill materials are utilized for European and Asian lacquerware. Losses caused by damage to the lacquer surface can be structural or aesthetic. Losses should only be filled if the surrounding areas are stable, without potential of damage from the fill material. Trained Eastern conservators may choose to utilise Asian Lacquer as a fill for losses, while Western conservators may use alternate materials such as waxes, polyester resins and epoxy resins. Completed fills can then be inpainted to match the surrounding lacquer surface.[11]
Online Resources and Case Studies
Online Resources
Institution | Resource | Link |
---|---|---|
Asian Art Museum of San Francisco | Conservation of Asian Lacquer | http://www.asianart.org/collections/conservation-of-asian-lacquer |
American Institute for Conservation | Art Conservation Wiki - Lacquer | http://www.conservation-wiki.com/wiki/Lacquer |
The Getty Institute | Characterization of Asian and European Lacquers | http://www.getty.edu/conservation/our_projects/science/lacquers/ |
Case Studies
Institution | Conservation Treatment | Link |
---|---|---|
Victoria and Albert Museum | Conservation of the Mazarin Chest | http://www.vam.ac.uk/page/c/conservation-of-the-mazarin-chest/ |
Historic New England | Conservation of a Lacquer Sewing Table | http://www.historicnewengland.org/about-us/whats-new/inside-the-conservation-lab-asian-lacquer-treatment |
References
- 1 2 3 4 "Lacquer - Wiki". www.conservation-wiki.com. Retrieved 2016-04-18.
- 1 2 "Bishop Museum Art Conservation Handout: Lacquer" (PDF).
- 1 2 3 "Asian Art Museum | Conservation of Asian Lacquer". www.asianart.org. Retrieved 2016-04-19.
- ↑ Fleming, Stuart (1987-01-01). "SCIENCE SCOPE: Japanese Urushi: The Finishing Touch". Archaeology. 40 (4): 62–77. JSTOR 41731914.
- 1 2 Webb, Marianne (2000). Lacquer: Technology and conservation: A comprehensive guide to the technology and conservation of Asian and European lacquer. Oxford: Butterworth-Heinemann.
- 1 2 3 [email protected], Victoria and Albert Museum, Online Museum, Web Team,. "The Conservation of Oriental Lacquer". www.vam.ac.uk. Retrieved 2016-04-20.
- ↑ Kisluk-Grosheide, Danielle O. (1984-01-01). "A Japanned Cabinet in the Metropolitan Museum of Art". Metropolitan Museum Journal. 19/20: 85–95. doi:10.2307/1512814. ISSN 0077-8958.
- ↑ "URUSHI-KOBO in EUROPE - CONSERVATION/ RESTORATION". www.urushi-kobo.com. Retrieved 2016-04-19.
- ↑ [email protected], Victoria and Albert Museum, Online Museum, Web Team,. "The development of English black japanning 1620-1820". www.vam.ac.uk. Retrieved 2016-04-19.
- 1 2 3 COUEIGNOUX, CATHERINE (2009-01-01). "AQUEOUS CLEANING OF PHOTODEGRADED EAST ASIAN LACQUER: A CASE STUDY". Journal of the American Institute for Conservation. 48 (1): 51–67. JSTOR 27784652.
- 1 2 Webb, Marianne (1998-01-01). "Methods and Materials for Filling Losses on Lacquer Objects". Journal of the American Institute for Conservation. 37 (1): 117–133. doi:10.2307/3179915. JSTOR 3179915.
- ↑ [email protected], Victoria and Albert Museum, Online Museum, Web Team,. "A Collaborative Approach". www.vam.ac.uk. Retrieved 2016-04-23.
- ↑ "Museum Standards and Best Practices - Collections Stewardship". www.aam-us.org. Retrieved 2016-04-22.
- ↑ "Characterization of European and Asian Lacquers". www.getty.edu. Retrieved 2016-04-19.
- ↑ "Code of Ethics and Guidelines for Practice". www.conservation-us.org. Retrieved 2016-04-24.
- 1 2 3 4 5 Williams, Jane (2008). "Conservation of Asian Lacquer Case Studies at the Asian Art Museum of San Francisco" (PDF).
External links
- "Conservation of Japanese lacquer in Western collections – conserving". www.academia.edu. Retrieved 2016-04-24.
- Weintraub, S., Tsujimoto, K., & Sadae Y. Walters. (1979). Urushi and Conservation: The Use of Japanese Lacquer in the Restoration of Japanese Art. Ars Orientalis, 11, 39–62. Retrieved from http://www.jstor.org/stable/4629296
- Quin, John J. Urushi: The Technology of Japanese Lacquer. Portland, Or.: Caber, 1995.