Porous silicon
Porous silicon (abbreviated as "PS" or "pSi") is a form of the chemical element silicon that has introduced nanopores in its microstructure, rendering a large surface to volume ratio in the order of 500 m2/cm3.
History
Porous silicon was discovered by accident in 1956 by Arthur Uhlir Jr. and Ingeborg Uhlir at the Bell Labs in the U.S. At the time, the Ulhirs were in the process of developing a technique for polishing and shaping the surfaces of silicon and germanium. However, it was found that under several conditions a crude product in the form of thick black, red or brown film were formed on the surface of the material. At the time, the findings were not taken further and were only mentioned in Bell Lab's technical notes.[1]
Despite the discovery of porous silicon in the 1950s, the scientific community was not interested in porous silicon until the late 1980s. At the time, Leigh Canham – while working at the Defence Research Agency in England – reasoned that the porous silicon may display quantum confinement effects.[2] The intuition was followed by successful experimental results published in 1990. In the published experiment, it was revealed that silicon wafers can emit light if subjected to electrochemical and chemical dissolution.
The published result stimulated the interest of the scientific community in its non-linear optical and electrical properties. The growing interest was evidenced in the number of published work concerning the properties and potential applications of porous silicon. In an article published in 2000, it was found that the number of published work grew exponentially in between 1991 and 1995.[3]
In 2001, a team of scientists at the Technical University of Munich inadvertently discovered that hydrogenated porous silicon reacts explosively with oxygen at cryogenic temperatures, releasing several times as much energy as an equivalent amount of TNT, at a much greater speed. (An abstract of the study can be found below.) Explosion occurs because the oxygen, which is in a liquid state at the necessary temperatures, is able to oxidize through the porous molecular structure of the silicon extremely rapidly, causing a very quick and efficient detonation. Although hydrogenated porous silicon would probably not be effective as a weapon, due to its functioning only at low temperatures, other uses are being explored for its explosive properties, such as providing thrust for satellites.
Fabrication of porous silicon
Fabrication of porous silicon may range from initial formation through stain-etching or by forming an anodization cell. Drying, storage of porous silicon, and surface modification are needed afterwards. If anodization in an aqueous solution is used to form microporous silicon, the material is commonly treated in ethanol immediately after fabrication, to avoid damage to the structure that results due to the stresses of the capillary effect of the aqueous solution.[4]
Anodization
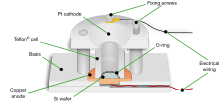
One method of introducing pores in silicon is through the use of an anodization cell. A possible anodization cell employs platinum cathode and silicon wafer anode immersed in hydrogen fluoride (HF) electrolyte. Recently, inert diamond cathodes are used to avoid metallic impurities in the electrolyte and inert diamond anodes form an improved electrical back plate contact to the silicon wafers. Corrosion of the anode is produced by running electric current through the cell. It is noted that the running of constant DC is usually implemented to ensure steady tip-concentration of HF resulting in a more homogeneous porosity layer although pulsed current is more appropriate for the formation of thick silicon wafers bigger than 50 µm.[5]
It was noted by Halimaoui that hydrogen evolution occurs during the formation of porous silicon.
When purely aqueous HF solutions are used for the PS formation, the hydrogen bubbles stick to the surface and induce lateral and in-depth inhomogeneity
The hydrogen evolution is normally treated with absolute ethanol in concentration exceeding 15%. It was found that the introduction of ethanol eliminates hydrogen and ensures complete infiltration of HF solution within the pores. Subsequently, uniform distribution of porosity and thickness is improved.
Stain etching
It is possible to obtain porous silicon through stain-etching with hydrofluoric acid, nitric acid and water. A publication in 1957 revealed that stain films can be grown in dilute solutions of nitric acid in concentrated hydrofluoric acid.[6] Porous silicon formation by stain-etching is particularly attractive because of its simplicity and the presence of readily available corrosive reagents; namely nitric acid (HNO3) and hydrogen fluoride (HF). Furthermore, stain-etching is useful if one needs to produce a very thin porous Si films.[7] A publication in 1960 by R. J. Archer revealed that it is possible to create stain films as thin as 25 Å through stain-etching with HF-HNO3 solution.
Bottom-Up Synthesis
Porous silicon can be synthesized chemically from silicon tetrachloride, using self-forming salt byproducts as templates for pore formation. The salt templates are later removed with water.[8]
Drying of porous silicon
Porous silicon is systematically prone to presence of cracks when the water is evaporated. The cracks are particularly evident in thick or highly porous silicon layers.[9] The origin of the cracks has been attributed to the large capillary stress due to the minute size of the pores. In particular, it has been known that cracks will appear for porous silicon samples with thickness larger than a certain critical value. Bellet concluded that it was impossible to avoid cracking in thick porous silicon layers under normal evaporating conditions. Hence, several appropriate techniques have been developed to minimize the risk of cracks formed during drying.
- Supercritical drying
Supercritical drying is reputed to be the most efficient drying technique but is rather expensive and difficult to implement. It was first implemented by Canham in 1994 and involves superheating the liquid pore above the critical point to avoid interfacial tension.[10]
- Freeze drying
Freeze drying procedure was first documented around 1996.[11] After the formation of porous silicon, the sample is frozen at a temperature of about 200 K and sublimed under vacuum.[12]
- Pentane drying
The technique uses pentane as the drying liquid instead of water. In doing so the capillary stress is reduced because pentane has a lower surface tension than water.[13]
- Slow evaporation
Slow evaporating technique can be implemented following the water or ethanol rinsing. It was found that slow evaporation decreased the trap density
Surface modification of porous silicon
The surface of porous silicon may be modified to exhibit different properties. Often, freshly etched porous silicon may be unstable due to the rate of its oxidation by the atmosphere or unsuitable for cell attachment purposes. Therefore, it can be surface modified to improve stability and cell attachment
Surface modification improving stability
Following the formation of porous silicon, its surface is covered with covalently bonded hydrogen. Although the hydrogen coated surface is sufficiently stable when exposed to inert atmosphere for a short period of time, prolonged exposure render the surface prone to oxidation by atmospheric oxygen. The oxidation promotes instability in the surface and is undesirable for many applications. Thus, several methods were developed to promote the surface stability of porous silicon.
An approach that can be taken is through thermal oxidation. The process involves heating the silicon to a temperature above 1000 C to promote full oxidation of silicon. The method reportedly produced samples with good stability to aging and electronic surface passivation.[14]
Porous silicon exhibits a high degree of biocompatibility. The large surface area enables organic molecules to adhere well. It degrades to Orthosillicic acid (H4SiO4),[15] which causes no harm to the body. This has opened potential applications in medicine such as a framework of the growth of bone.
Surface modification improving cell adhesion
Surface modification can also affect properties that promote cell adhesion. One particular research in 2005 studied the mammalian cell adhesion on the modified surfaces of porous silicon. The research used rat PC12 cells and Human Lens Epithelial (HLE) cells cultured for four hours on the surface modified porous silicon. Cells were then stained with vital dye FDA and observed under fluorescence microscopy. The research concluded that "amino silanisation and coating the pSi surface with collagen enhanced cell attachment and spreading".[16]
Classification of porous silicon
Porosity
Porosity is defined as the fraction of void within the pSi layer and can be determined easily by weight measurement.[5] During formation of porous silicon layer through anodization, the porosity of a wafer can be increased through increasing current density, decreasing HF concentration and thicker silicon layer. The porosity of porous silicon may range from 4% for macroporous layers to 95% for mesoporous layers. A study by Canham in 1995 found that "a 1 µm thick layer of high porosity silicon completely dissolved within a day of in-vitro exposure to a simulated body fluid".[17] It was also found that a silicon wafer with medium to low porosity displayed more stability. Hence, the porosity of porous silicon is varied depending on its potential application areas.
Pore size
The porosity value of silicon is a macroscopic parameter and doesn’t yield any information regarding the microstructure of the layer. It is proposed that the properties of a sample are more accurately predicted if the pore size and its distribution within the sample can be obtained. Therefore, porous silicon has been divided into three categories based on the size of its pores; macroporous, mesoporous, and microporous.
Type | Microporous | Mesoporous | Macroporous |
---|---|---|---|
Pore width (Nanometer) | less than 2 | Between 2 and 50 | Larger than 50 |
Key characteristic of porous silicon
Highly controllable properties
Porous silicon studies conducted in 1995 showed that the behavior of porous silicon can be altered in between "bio-inert", "bioactive" and "resorbable" by varying the porosity of the silicon sample.[17] The in-vitro study used simulated body fluid containing ion concentration similar to the human blood and tested the activities of porous silicon sample when exposed to the fluids for prolonged period of time. It was found that high porosity mesoporous layers were completely removed by the simulated body fluids within a day. In contrast, low to medium porosity microporous layers displayed more stable configurations and induced hydroxyapatite growth.
Bioactive
The first sign of porous silicon as a bioactive material was found in 1995. In the conducted study, it was found that hydroxyapatite growth was occurring on porous silicon areas. It was then suggested that "hydrated microporous Si could be a bioactive form of the semiconductor and suggest that Si itself should be seriously considered for development as a material for widespread in vivo applications."[17] Another paper published the finding that porous silicon may be used a substrate for hydroxyapatite growth either by simple soaking process or laser-liquid-solid interaction process.[18]
Since then, in-vitro studies have been conducted to evaluate the interaction of cells with porous silicon. A 1995 study of the interaction of B50 rat hippocampal cells with porous silicon found that B50 cells have clear preference for adhesion to porous silicon over untreated surface. The study indicated that porous silicon can be suitable for cell culturing purposes and can be used to control cell growth pattern.[19]
Non-toxic waste product
Another positive attribute of porous silicon is the degradation of porous silicon into monomeric silicic acid (SiOH4). Silicic acid is reputed to be the most natural form of element in the environment and is readily removed by kidneys.
The human blood plasma contains monomeric silicic acid at levels of less than 1 mg Si/l, corresponding to the average dietary intake of 20–50 mg/day. It was proposed that the small thickness of silicon coatings presents minimal risk to a toxic concentration being reached. The proposal was supported by an experiment involving volunteers and silicic-acid drinks. It was found that concentration of the acid rose only briefly above the normal 1 mg Si/l level and was efficiently expelled by urine excretion.[20]
Superhydrophobicity
The simple adjustment of pore morphology and geometry of porous silicon also offers a convenient way to control its wetting behavior. Stable ultra- and superhydrophobic states on porous silicon can be fabricated and used in lab-on-a-chip, microfluidic devices for the improved surface-based bioanalysis.[21]
Optical properties
pSi demonstrates optical properties based on porosity and the medium inside the pores. The effective refractive index of pSi is determined by the porosity and refractive index of the medium inside the pores. If the refractive index of the medium inside pores is high, the effective refractive index of pSi will be high as well. This phenomenon causes the spectrum to shift towards longer wavelength.[22]
See also
References
- ↑ Canham, Leigh T. (10 April 1993). "A glowing future for silicon: Chips and circuits could work much faster if they used light to communicate with each other. Fragile layers of porous silicon could be just the thing to let them do it". New Scientist. Retrieved February 25, 2013.
- ↑ Sailor Research Group 17 February 2003, Introduction to Porous Si, Sailor research group at UCSD, Department of Chemistry, University of California.
- ↑ Parkhutik, Vera (2000). Journal of Porous Materials. 7: 363. doi:10.1023/A:1009643206266. Missing or empty
|title=
(help) - ↑ Porous Silicon Fabrication, retrieved April 3, 2016
- 1 2 Halimaoui A. 1997, "Porous silicon formation by anodization", in Properties of Porous Silicon. Canham, L. T., Institution of Engineering and Technology, London, ISBN 0-85296-932-5 pp. 12–22.
- ↑ Archer, R. (1960). "Stain films on silicon". Journal of Physics and Chemistry of Solids. 14: 104. Bibcode:1960JPCS...14..104A. doi:10.1016/0022-3697(60)90215-8.
- ↑ Coffer J. L. 1997, "Porous silicon formation by stain etching", in Properties of Porous Silicon, Canham, L. T., Institution of Engineering and Technology, London, ISBN 0-85296-932-5 pp. 23–28.
- ↑ http://www.nature.com/ncomms/2014/140410/ncomms4605/full/ncomms4605.html
- ↑ Bellet D. 1997, "Drying of porous silicon", in Properties of Porous Silicon, Canham, L. T., Institution of Engineering and Technology, London, ISBN 0-85296-932-5 pp. 38–43.
- ↑ Canham, L. T.; Cullis, A. G.; Pickering, C.; Dosser, O. D.; Cox, T. I.; Lynch, T. P. (1994). "Luminescent anodized silicon aerocrystal networks prepared by supercritical drying". Nature. 368 (6467): 133. Bibcode:1994Natur.368..133C. doi:10.1038/368133a0.
- ↑ Amato, G. (1996). "Porous silicon via freeze drying". Materials Letters. 26 (6): 295. doi:10.1016/0167-577X(95)00244-8.
- ↑ Scott, S. M.; James, D.; Ali, Z.; Bouchaour, M. (2004). "Effect of drying on porous silicon". Journal of Thermal Analysis and Calorimetry. 76 (2): 677. doi:10.1023/B:JTAN.0000028047.00086.ef.
- ↑ Wang, Fuguo; Song, Shiyong; Zhang, Junyan (2009). "Surface texturing of porous silicon with capillary stress and its superhydrophobicity". Chemical Communications (28): 4239. doi:10.1039/b905769b.
- ↑ Chazalviel J. N., Ozanam F. 1997, "Surface modification of porous silicon", in Properties of Porous Silicon, Canham, L. T., Institution of Engineering and Technology, London, ISBN 0-85296-932-5 pp. 59–65.
- ↑ Tantawi et. al. Porous silicon membrane for investigation of transmembrane proteins, Journal of Superlattices and Microstructures, Vol. 58, 2013, pages 78-80
- ↑ Low, S. P.; Williams, K. A.; Canham, L. T.; Voelcker, N. H. (2006). "Evaluation of mammalian cell adhesion on surface-modified porous silicon". Biomaterials. 27 (26): 4538–46. doi:10.1016/j.biomaterials.2006.04.015. PMID 16707158.
- 1 2 3 Canham, Leigh T. (1995). "Bioactive silicon structure fabrication through nanoetching techniques". Advanced Materials. 7 (12): 1033. doi:10.1002/adma.19950071215.
- ↑ Pramatarova, L.; Pecheva, E.; Dimovamalinovska, D.; Pramatarova, R.; Bismayer, U.; Petrov, T.; Minkovski, N. (2004). "Porous silicon as a substrate for hydroxyapatite growth". Vacuum. 76 (2–3): 135. doi:10.1016/j.vacuum.2004.07.004.
- ↑ Sapelkin, A.; Bayliss, S.; Unal, B.; Charalambou, A. (2006). "Interaction of B50 rat hippocampal cells with stain-etched porous silicon". Biomaterials. 27 (6): 842–6. doi:10.1016/j.biomaterials.2005.06.023. PMID 16098578.
- ↑ Canham, L. T., Aston R. (July 2001). "Will a chip every day keep the doctor away?" (PDF). Physics World. 14 (7): 27–32.
- ↑ Ressine, A.; Marko-Varga, G.; Laurell, T. (2007). "Porous silicon protein microarray technology and ultra-/superhydrophobic states for improved bioanalytical readout". Biotechnology Annual Review. 13: 149–200. doi:10.1016/S1387-2656(07)13007-6. PMID 17875477.
- ↑ Ouyang, Huimin (2005). "Biosensing using porous silicon photonic bandgap structures". 6005: 600508. doi:10.1117/12.629961.
Further reading
- Feng Z.C.; Tsu R., eds. (1994). Porous Silicon. Singapore: World Scientific. ISBN 981-02-1634-3.
- Kovalev D.; Timoshenko V. Y.; Künzner N.; Gross E.; Koch F. (August 2001). "Strong explosive interaction of hydrogenated porous silicon with oxygen at cryogenic temperatures". Phys. Rev. Lett. 87 (6): 068301. Bibcode:2001PhRvL..87f8301K. doi:10.1103/PhysRevLett.87.068301. PMID 11497868.