Power loom
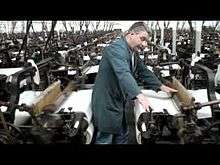
A power loom is a mechanised loom powered by a line shaft, and was one of the key developments in the industrialization of weaving during the early Industrial Revolution. The first power loom was designed in 1784 by Edmund Cartwright and first built in 1785. It was refined over the next 47 years until a design by Kenworthy and Bullough made the operation completely automatic.
By 1850 there were 260,000 in operation in England. Fifty years later came the Northrop Loom that would replenish the shuttle when it was empty and this replaced the Lancashire loom.
Shuttle looms

The huge components of the loom are the warp beam, heddles, harnesses, shuttle, reed and takeup roll. In the loom, yarn processing includes shedding, picking, battening and taking-up operations.
- Shedding. Shedding is the raising of the warp yarns to form a loop through which the filling yarn, carried by the shuttle, can be inserted. The shed is the vertical space between the raised and unraised warp yarns. On the modern loom, simple and intricate shedding operations are performed automatically by the heddle or heald frame, also known as a harness. This is a rectangular frame to which a series of wires, called heddles or healds, are attached. The yarns are passed through the eye holes of the heddles, which hang vertically from the harnesses. The weave pattern determines which harness controls which warp yarns, and the number of harnesses used depends on the complexity of the weave. Two common methods of controlling the heddles are dobbies and a Jacquard Head.
- Picking. As the harnesses raise the heddles or healds, which raise the warp yarns, the shed is created. The filling yarn is inserted through the shed by a small carrier device called a shuttle. The shuttle is normally pointed at each end to allow passage through the shed. In a traditional shuttle loom, the filling yarn is wound onto a quill, which in turn is mounted in the shuttle. The filling yarn emerges through a hole in the shuttle as it moves across the loom. A single crossing of the shuttle from one side of the loom to the other is known as a pick. As the shuttle moves back and forth across the shed, it weaves an edge, or selvage, on e-ach side of the fabric to prevent the fabric from ravelling.
- Battening. As the shuttle moves across the loom laying down the fill yarn, it also passes through openings in another frame called a reed (which resembles a comb). With each picking operation, the reed presses or battens each filling yarn against the portion of the fabric that has already been formed. The point where the fabric is formed is called the fell. Conventional shuttle looms can operate at speeds of about 150 to 160 picks per minute.
With each weaving operation, the newly constructed fabric must be wound on a cloth beam. This process is called taking up. At the same time, the warp yarns must be let off or released from the warp beams. To become fully automatic, a loom needs a filling stop motion which will brake the loom, if the weft thread breaks.
Operation
Operation of weaving in a textile mill is undertaken by a specially trained operator known as a weaver. Weavers are expected to uphold high industry standards, and are tasked with monitoring anywhere from ten, to as many as thirty separate looms at any one time. During their operating shift, weavers will first utilize a wax pencil or crayon to sign their initials onto the cloth to mark a shift change, and then walk along the cloth side (front) of the looms they tend, gently touching the fabric as it comes from the reed. This is done to feel for any broken "picks" or filler thread. Should broken picks be detected, the weaver will disable the machine and undertake to correct the error, typically by replacing the bobbin of filler thread in as little time as possible. They are trained that, ideally, no machine should stop working for more than one minute, with faster turn around times being preferred.
Once the weaver has made their circuit of the front of the machines, they will then circle around to the back. At this point they will gently stroke their hand over the raised metal "tells" on the back of the machine. These tells, located over a special metal circuit, are held up by the tension of the thread coming from the warp. Should the warp thread be broken, the tells will drop and cause the machine to stop working. However, it is possible for them to become stuck in the upward position, and by doing so create problems in the weaving. By gently touching the tells, then, it is possible for the weaver to find tells which have become stuck in the up position, and correct the error. As with pick breaks, the weavers are trained to keep the machines running as much as possible; with speedy knot tying and correction being stressed. In this situation, they are expected to take less than a minute, with the mean ideal being ten to thirty seconds, to correct a break. The weaver also watches for warps that are about to run out, or problems in the warp itself which were not detected in the slashing process. Typically, weavers can expect to make several dozen circuits of their machines a night, with most of their time spent ensuring the quality of the cloth and the company standards of production.
History
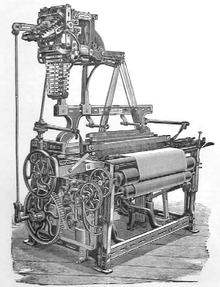
Edmund Cartwright patented a power loom in 1785. This used water as power instead of human power which sped up the weaving process. Weavers were able to use all the thread that spinners could produce.[1] It was to be forty years before his ideas were modified into a reliable automatic loom. Cartwright was not the first man to design an automatic loom, this had been done in 1678 by M. de Gennes in Paris, and again by Vaucanson In 1745, but these never developed and were forgotten. Those designs preceded John Kay's invention of the flying shuttle and they passed the shuttle through the shed using levers.
It was not a commercially successful machine. His ideas were licensed first by Grimshaw, of Manchester who built a small steam-powered weaving factory in Manchester in 1790. The looms had to be stopped to dress the warp, but the factory burnt down before anything could be learned.
- Series of initial inventors
A series of inventors incrementally improved all aspects of the three principle processes and the ancillary processes.
- Grimshaw 1790 Manchester- dressing the warp
- Austin 1789, 1790 -dressing the warp, 200 looms produced for Monteith of Pollockshaws 1800
- Thomas Johnson, 1803, Bredbury- dressing frame: Factory for 200 Steam Looms on Manchester 1806, and two factories at Stockport 1809. One at Westhoughton, Lancashire 1809.
- William Radcliffe of Stockport 1802- improved take up mechanism
- John Todd of Burnley 1803- a heald roller and new shedding arrangements, the healds were corded to treadles actuated by cams on the second shaft.
- William Horrocks of Stockport 1803- The frame was still wooden but the lathe was pendant from the frame and operated by cams on the first shaft, the shedding was operated by cams on the second shaft, the take up motion was copied from Radcliffe.
- Peter Marsland 1806- improvements to the lathe motion to counteract poor picking
- William Cotton 1810- improvements to the letting off motion
- William Horrocks 1813 -Horrocks Loom Modifications to the lathe motion- improving on Marsland
- Peter Ewart 1813 -a use of pneumatics
- Joseph and Peter Taylor 1815 -double beat foot lathe for heavy cloths
- Paul Moody 1815- produces the first power loom in North America. Exporting a UK loom would have been illegal.
- John Capron and Sons 1820- installed the first power looms for woolens in North America at Uxbridge, Massachusetts.
- William Horrocks 1821 -a system to wet the warp and weft during use, improving the effectiveness of the sizing
- Richard Roberts 1830, Roberts Loom, These improvements were a geared take up wheel and tappets to operate multiple heddles[2]
- Stanford, Pritchard and Wilkinson- patented a method to stop on the break of weft or warp. It was not used.
- William Dickinson of Blackburn Blackburn Loom the modern overpick loom
- Further useful improvements
There now appear a series of useful improvements that are contained in patents for useless devices
- Hornby, Kenworthy and Bullough of Blackburn 1834- the vibrating or fly reed
- John Ramsbottom and Richard Holt of Todmorden 1834- a new automatic weft stopping motion
- James Bullough of Blackburn 1835- improved automatic weft stopping motion and taking up and letting off arrangements
- Andrew Parkinson 1836- improved stretcher (temple).
- William Kenworthy and James Bullough 1841- trough and roller temple (became the standard), A simple stop-motion.[3]
At this point the loom has become automatic except for refilling weft pirns. The Cartwight loom weaver could work one loom at 120-130 picks per minute- with a Kenworthy and Bullough's Lancashire Loom, a weaver can run up to six looms working at 220-260 picks per minute- thus giving 12 times more through put.
Looms and the Manchester context
The development of the power loom in and around Manchester was not a coincidence. Manchester has been a centre for Fustians by 1620 and acted as a hub for other Lancashire towns, so developing a communication network with them. It was an established point of export using the meandering River Mersey, and by 1800 it had a thriving canal network, with links to the Ashton Canal, Rochdale Canal the Peak Forest Canal and Manchester Bolton & Bury Canal. The fustian trade gave the towns a skilled workforce that was used to the complicated Dutch looms, and was perhaps accustomed to industrial discipline. While Manchester became a spinning town, the towns around were weaving towns producing cloth by the putting out system. The business was dominated by a few families who had the capital needed for the investment in new mills, and buy hundreds of looms. The mills were built along the new canals so immediately had access to their markets. Spinning developed first and, until 1830, the handloom was still more important economically than the power loom when the roles reversed.[4] Because of the economic growth of Manchester, a new industry of precision machine tool engineering was born and here were the skills needed to build the precision mechanisms of a loom.
Adoption
Number of Looms in UK[5] Year 1803 1820 1829 1833 1857 Looms 2,400 14,650 55,500 100,000 250,000
Draper's strategy was to standardise on a couple of models which it mass-produced. The lighter E-model of 1909 was joined in the 1930 by the heavier X-model. Continuous fibre machines, say for rayon, which was more break-prone, needed a specialist loom. This was provided by the purchase of the Stafford Loom Co. in 1932, and using their patents a third loom the XD, was added to the range. Because of their mass production techniques they were reluctant and slow to retool for new technologies such as shuttleless looms.[6]
Decline and reinvention
Originally, power looms used a shuttle to throw the weft across, but in 1927 the faster and more efficient shuttleless loom came into use. Sulzer Brothers, a Swiss company had the exclusive rights to shuttleless looms in 1942, and licensed the American production to Warner & Swasey. Draper licensed the slower rapier loom. Today, advances in technology have produced a variety of looms designed to maximise production for specific types of material. The most common of these are Sulzer shuttleless weaving machines, rapier looms, air-jet looms and water-jet looms.[7]
Social and economic implications
The power loom reduced demand for skilled handweavers, initially causing reduced wages and unemployment. Protests followed its introduction. For example, in 1816 two thousand rioting Calton weavers tried to destroy power loom mills and stoned the workers.[8] In the longer term, by making cloth more affordable the power loom increased demand and stimulated exports, causing a growth in industrial employment, albeit low-paid.[9] The power loom also opened up opportunities for women mill workers.[10] A darker side of the power loom's impact was the growth of employment of children in power loom mills.[11]
Dangers
When operated by a skilled and attentive weaver, looms are not dangerous by themselves. However, there are a number of inherent dangers in the machines, to which inattentive or poorly trained weavers can fall victim. The most obvious is the moving reed, the frames which hold the heddles and the "pinch" or "sand" roll utilized to keep the cloth tight as it passes over the front of the machine and onto the doff roll. The most common injury in weaving is pinched fingers from distracted or bored workers, though this is not the only such injury found. There are numerous accounts of weavers with long hair getting it tangled in the warp itself and having their scalp pulled away from the skull, or large chunks of hair pulled off.[12] As a result of this, it has become industry standard for companies to require weavers to either keep hair up and tied, or to keep their hair short so as not to allow it to become tangled. Also, due to possible pinch points on the front of machines, loose, baggy clothing is prohibited. One complication for weavers, in the terms of safety, is the loud nature in which weave mills operate. Because of this, it is nearly impossible to hear a person calling for help when entangled, and has led OSHA to outline specific guidelines[13] for companies to mitigate the chance of such circumstances from happening. However, even with such guidelines in place, injuries in textile production, due to the machines themselves, are still commonplace.
See also
- Dobby loom
- Jacquard loom
- Paul Moody
- Northrop Loom
- Textile manufacture during the Industrial Revolution
References
- ↑ Marsden 1895, p. 64
- ↑ Marsden 1895, pp. 70,71
- ↑ Marsden 1895, pp. 88–95
- ↑ Miller & Wild 2007, p. 10
- ↑ Hills 1993, p. 117
- ↑ Mass 1990
- ↑ Collier 1970, p. 111
- ↑ Anna Clark (1997), The struggle for the breeches: gender and the making of the British working class, University of California Press, p. 32ff, ISBN 0520208838
- ↑ Geoffrey Timmins (1993), The last shift: the decline of handloom weaving in nineteenth-century Lancashire, Manchester University Press ND, p. 19ff, ISBN 0719037255
- ↑ Gail Fowler Mohanty (2006), Labor and laborers of the loom: mechanization and handloom weavers, 1780-1840, CRC Press, p. 114ff, ISBN 0415979021
- ↑ Neil J. Smelser (2006), Social Change in the Industrial Revolution: An Application of Theory to the British Cotton Industry, Taylor & Francis, pp. 208–209, ISBN 0415381371
- ↑ "Lucy Larcom (1824-1893)". National Women's History Museum. Retrieved 2014-03-25.
- ↑ http://www.ilo.org/oshenc/part-xiv/textile-goods-industry/item/888-weaving-and-knitting
Bibliography
- Collier, Ann M (1970), A Handbook of Textiles, Pergamon Press, p. 258, ISBN 0-08-018057-4
- Hills, Richard Leslie (1993), Power from Steam: A History of the Stationary Steam Engine, Cambridge University Press, p. 244, ISBN 9780521458344, retrieved January 2009 Check date values in:
|access-date=
(help) - Jenkins, Geraint (1972), Geraint Jenkins, ed., The wool textile industry in Great Britain, London & Boston: Routledge Keegan Paul, ISBN 0-7100-69790
- Marsden, Richard (1895), Cotton Weaving: Its Development, Principles, and Practice, George Bell & Sons, p. 584, retrieved Feb 2009 Check date values in:
|access-date=
(help) - Mass, William (1990), "The Decline of a Technology Leader:Capability, strategy and shuttleless Weaving" (PDF), Business and Economic History, ISSN 0894-6825.
- Miller, I; Wild (2007), Rachel Newman, ed., A& G Murray and the Cotton Mills of Ancoats, Meeting House Lane, Lancaster: Oxford Archeology North, ISBN 978-0-904220-46-9 Cite uses deprecated parameter
|coauthors=
(help)