Salt industry in Syracuse, New York
The salt industry has a long history in and around Syracuse, New York. Jesuit missionaries visiting the region in 1654 were the first to report salty brine springs around the southern end of "Salt Lake," known today as Onondaga Lake.[1] Later, the Treaty of Fort Stanwix (1784) and designation of the area by the State of New York as the "Onondaga Salt Springs Reservation" provided the basis for commercial salt production from the late 18th century through the early 20th century.[2] The salt springs extended around much of Onondaga Lake, originating in the town of Salina and passing through Geddes and Liverpool to the mouth of Ninemile Creek, a distance of almost nine miles.[1] The majority of salt used in the United States in the 19th century came from Syracuse.[3] Even today, Syracuse is sometimes known as "the Salt City."
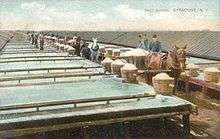
History
A series of deep and shallow aquifer systems in the Onondaga Creek Valley provided the brine that stimulated early growth in the Syracuse area. Many settlers came to the region to mine the salt and earn a better standard of living for their families.[4]
Throughout the years, a wide variety of coarse salt produced from boiling and refined salt produced by the solar method were manufactured on the Onondaga Salt Springs Reservation including; dairy, table, common, fine and fertilizing salts.[5]
Salt, limestone and shale
Thick layers of shale beneath the Syracuse area were formed over a period of 300 to 500 million years ago. On the East Coast of North America, two landmasses collided and formed a large mountain range. A large shallow depression to the west formed an inland sea. Precipitation and runoff over millions of years gradually eroded the mountain range and sediment, in the form of mud, consolidated into thick layers of what later hardened into shale.[4]
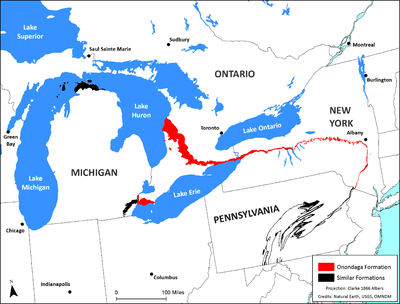
The northern shore of the inland sea was situated in Tully, about five miles south the city. The salt was formed after evaporation from the shallowest areas left layers of evaporites or salts. These included calcium carbonate (calcite), calcium sulfate (gypsum) and sodium chloride (halite), also known as common salt.[4]
During the Ice Age, the processes of glaciation followed by deglaciation eroded and reshaped the bedrock foundation that consists of limestone, shale and evaporite deposits. The gradual shedding of glacial deposits created the aquifer that provide a "hydraulic connection" between the halite deposits south of the city in Tully and the salt springs at the southeastern end of Onondaga Lake.[4]
The resulting Onondaga Formation was the source of salt belonging to the Onondaga salt-group which extends from the Hudson Valley through Syracuse to Wyoming County, New York, where salt wells were established in the early 1880s. From there, it continues through Southern Ontario to Saginaw, Michigan, and extends as far west as Wisconsin and Iowa.[6]
Salt springs are one of three sources from which salt is obtained; rock salt (fossil salt), sea water and salt brine which is derived from springs, lakes, or wells.[7] The brine obtained from the lake is one quality, but it yields two qualities of salt by different processes of evaporation; solar heat being used in the evaporation of coarse salt and thermal heat (boiling) in the evaporation of refined salt.[8]
Jesuit missionaries
“ | We tested the water of a spring, which the Indians are afraid to drink, saying that it is inhabited by a demon, which makes it foul. I found the fountain of salt water, from which we evaporated a little salt as natural as that from the sea, some of which we shall carry to Quebec. - Father Simon Le Moyne from his diary in 1654 [8] | ” |
The salt springs of Onondaga Lake were well known to the Jesuit missionaries. Early in the 16th century a number of Spaniards traveled from Florida in order to examine a "mysterious white substance" that covered the ground.[9]
On August 5, 1654, Father Simon Le Moyne, a French Jesuit missionary, arrived in the Onondaga village. During his short stay, Le Moyne drank from a spring which the Onondagas believed to be tainted due to an evil spirit.[10] Unlike the Onondagas who considered the salt springs evil, the French instead, recognized the intrinsic value of the salt.[10]
Dutch at New Amsterdam
By 1660, the Dutch at New Amsterdam and Fort Orange, Albany, New York, were in receipt of information that "salt grew out of the ground," however, they refused to believe it.[9]
British interest
The British began to take an active interest in the land around Onondaga Lake in the early 18th century. They befriended the Onondagas by giving them guns, which were highly prized.
British agent, Sir William Johnson, acquired 200,000 acres (810,000,000 m2) of land in the Mohawk country near present-day Johnstown, New York. In 1751, Johnson heard that the French intended on securing a military post in the vicinity of the salt springs. He discussed the consequences of that action with the Onondagas and proposed that they grant him rights to all of Onondaga Lake and a 2 miles (3.2 km) band of land around it. The Onondagas agreed and were paid £350 sterling.[10]
The deed made in 1773 by Sir William Johnson with the Onondaga chiefs was declared invalid in September 1788.[9]
Presbyterian missionaries
In 1776, Presbyterian missionary, Samuel Kirkland, from Scotland, who had come to Central New York to teach the Seneca and Oneida people, became interested in the Syracuse "salt lands" and notified General Philip Schuyler about them. At the following session of the Continental Congress, Schuyler observed that the springs could be "improved to advantage" provided someone familiar with salt boiling "could attend to it," however, Congress failed to act on the suggestion and 11 years passed before any action was taken.[9]
Onondaga Salt Springs reservation
The Treaty of Fort Stanwix (1784) transferred lands around Onondaga Lake from the Onondaga Nation to local salt producers with the stipulation that the land would be used to produce salt "for the common use of everyone." As a result of the treaty, the area was designated by the State as the Onondaga Salt Springs Reservation.[4]
The salt works were shaped in a crescent in the salt marshes bordering the southeastern shore of Onondaga Lake and covered nearly 1,000 acres (4,000,000 m2). By 1872, the reservation occupied 750 acres (3,000,000 m2) and private individuals owned about 200 acres (810,000 m2) with the remainder "waste land."[11] The salt reservation was approximately 9 miles (14 km) long by 11 miles (18 km) wide.[12]
Early settlers
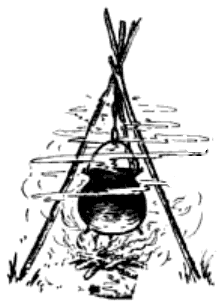
The springs remained in the possession of the Onondaga Indians until after the Revolutionary War. Some "white" settlers were "in the habit of making small quantities of salt for their personal use." They would boil the salt in "open kettles" suspended over fire from crotched sticks and a cross pole.[8] Two escaped slaves were reported boiling brine in brass kettles and selling the salt to the Onondaga Indians in 1774.[13]
While Onondaga County was slowly expanding, much activity was occurring at the salt springs. Men were arriving with their families to make a living from the salt industry. During 1788, early Syracuse pioneers, Asa Danforth and Comfort Tyler were the first to arrive. The third settler arrived in 1789 and by 1792 six families had set up household. They lived and worked in an area east of lower Onondaga Lake called Salt Point, later known as Salina.[10]
John Danforth, brother of Asa Danforth, followed him to the area and settled in Liverpool, New York. He was also an early manufacturer of salt on the shores of Onondaga Lake.[12]
Swamp life
In the early days of salt manufacture, great labor was required to boil the salt and the living conditions in the swamp were almost unbearable.[2] The salt springs were located on the south end of the lake which was covered in swamps and bogs for much of the warm months of the year. Malaria was rampant and laborers and their families suffered the effects of fevers and nausea.[10]
In 1793, out of a total population of 33 people, 30 were sick and the following year the population had grown to 63, but 23 died that year. Those that made it through the summer and fall seasons, traded salt for food items such as meat, produce, flour, cheese and maple syrup during the winter months. Visitors to Salt Point in the winter arrived via Iroquois trails because the settlers did not yet have a system of roads.[10]
Commercial salt production
As time progressed, there was a "growing perception of the ease, profits and other advantages of the manufacture" which led to more extensive operations.[8] The first two men involved in commercial salt production at the salt springs were early settlers, Asa Danforth and Comfort Tyler. Both were Revolutionary War veterans who settled on land they obtained from a grant from the newly formed government of the United States. Both men arrived at the salt springs during 1788 and began salt production in 1789 when Danforth carried a five-gallon pail kettle from his residence at Onondaga Hollow to Onondaga Salt Springs Reservation. He placed his coat on his head, inverted the kettle, and is said to have "carried it the whole distance without taking it off to rest."[14] Danforth noted that the first time he made salt he used a 15-gallon kettle and in nine hours he had "boiled down" about 30 pounds (14 kg) of salt.[2]
Comfort Tyler accompanied him, carrying an axe, chain and other necessary implements for the purpose of making a "suitable erection to boil salt." They set up two crotches and suspended their kettle on a chain around a pole between them. After a sufficient quantity was made, they would hide their implements in the bushes until needed again. The two continued the practice for another year until 1790.[14]
By 1798, salt houses were built of logs. Asa Danforth was a member of The Federal Company along with Jedediah Sanger, Daniel Keeler, Thomas Hart, Ebenezer Butler, Elisha Alvord and Hezekiah Olcott. The group organized in 1798 and the object of the company was to manufacture salt on a "stupendous scale." They erected a building capable of holding 32 kettles which were set in boiling blocks of four kettles each. Water was then pumped by hand, from a single shallow well, into reservoirs made of "dug out white wood logs" used for pipes."[14]
Before the construction of the Erie Canal, transportation was difficult. Oxen would travel through marshy land and haul out salt on stone-boats.[12]
Salt salinity
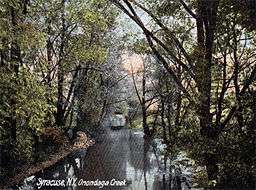
The brine from the reservation was extremely saline and in 1743 one gallon of water could be boiled down to one pound (0.45 kg) of salt. The salinity of water has been measured since the 1800s with a tool called the salometer which shows the percent saturation of salt in brine. The average reading of brine processed during the 1800s at the Onondaga Salt Springs Reservation measured between 74 °S through 78 °S. This would indicate the brine was as much as 78 percent saturated with salt.[4]
By pumping brine to the surface in the early 1800s, the amount of brine withdrawn from deep groundwater consequently increased. When the outlet of Onondaga Lake was lowered in 1822 for construction of the Erie Canal, this lowered the water table around the lake and "caused the brine springs to flow at higher rates than before." Over the course of many years, this resulted in freshwater from aquifers throughout Onondaga Creek Valley to recharge which diluted the deepwater brine. The less concentrated brine required more time to evaporate and the total yield was less than a more highly concentrated solution.[4]
In 1875, chemists reported that the strength of the brine was much greater than in 1874 due to two new wells which were sunk in the Syracuse district to replace the older, shallow wells. The shallow wells decreased in strength by 33 percent when pumped to their full capacity in a short period of time.[15]
During 1876, the State of New York was very concerned with the salinity of the brine relative to the cost of the fuel to reduce it to salt. There was increased competition in the salt industry with the strongest rivals in Michigan and Canada. Throughout the early 1870s, the State had funded the sinking of several new deep wells in order to increase the level of the average salinity of brine taken from the reservation. It was decided that if a sufficient number of deep wells were drilled that would yield a brine of 72 °S average strength, and the weak, shallow wells were abandoned entirely, the yield per ton of coal used would increase to 45 US bushels (1,600 l; 360 US dry gal; 350 imp gal) from the average 36 US bushels (1,300 l; 290 US dry gal; 280 imp gal) produced in the early 1870s. This realized an overall reduction in the price of coal from .10 cents to .08 cents per bushel of salt.[15]
State regulation
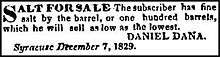
Many squatters who did not lease or own their land were producing salt by the late 1770s and the State of New York wanted to put an end to this illegal practice. Additionally, the State wanted to prevent a private company from forming a salt monopoly. They were also looking for a steady flow of income and salt appeared to be a good revenue source.[2]
In 1795, the Onondagas relinquished their common rights to the land around Onondaga Lake to the State.[10]
The first legislation was passed on April 1, 1797, and soon after, the State began the regulation of salt production.[2]
The New York State Legislature designated a 1 mile (1.6 km) wide strip of land around the northern half of the lake as the Onondaga Salt Springs Reservation. Laws were passed to regulate the methods used in the production including boiling and solar evaporation, storage, and sale of the salt. A duty collection was also established at .04 cents for every bushel of salt produced on the reservation. Although there was no charge for the brine itself, the State set the price of salt and required that salt be stored for a fee in government warehouses until it was sold. The State also had the right to certify the quantity and quality of all salt produced. In order to maintain a lease-hold, lessees were required to produce a minimum of ten bushels (56 pounds (25 kg) each) of salt per year for "every kettle or pan used" and were prohibited from charging more than .60 cents a bushel. They were also required to pay .04 cents per bushel tax in lieu of rent and an additional .01 cent for storage.[9]
Salt lots were surveyed and were made available for multi-year leases.[10] In 1797, the State split the land into salt lots, store lots and pasture lots, not to exceed 10 acres (40,000 m2) each,[9] which allowed private parties to dig wells and manufacture salt in consideration of payment of tax to the State.[8] The reservation now comprised 15,000 acres (61,000,000 m2) and the industry was a "benefit" to the State of New York for the next 100 years.[10]
The reservation reserved the right upon the expiration of the lease to renew for a term of seven years. They also gave the salt processors the ability to buy the property outright at its "true value."[9]
The same act authorized the appointment of a superintendent of the salt springs by the Governor, with the consent of the Council of Appointment which was a powerful Arbitrary Board. Salary was fixed at $800 per year and men appointed to the position were prohibited from having any interest in the salt springs. The first superintendents were James Duane and Robert Yates.[9] William Kirkpatrick (1769–1832), a medical doctor, moved to Salina in 1806. He subsequently became superintendent of the reservation and served from 1807 through 1810. He was appointed a second time, and served from 1810 through 1831.[16]
Many of the salt boilers did not want state involvement which they "deemed as interference." In order to avoid paying duty, many smuggled large amounts of salt, however, the superintendent "who had almost absolute power" could personally attest to each bushel produced.[10]
The State of New York owned and administered the Onondaga Salt Spring Reservation from 1797 to 1908, leasing out the land to individuals to build boiling blocks, solar sheds and other salt-making facilities. The enterprise consisted of a state-owned network of wells, rigs, pump houses, pipelines, reservoirs and wharves.[13]
The superintendent of the salt springs and his deputies would sink the wells, pump the water and distribute the water among the manufactories. They would also inspect the salt, weigh and brand the packages and collect the State duties.[11]
The original salt works was divided into four areas; Salt Point (later known as Salina), Geddes, Green Point and Liverpool. The Onondaga Salt Springs Reservation only included the Salt Point and the Geddes works. This meant the Green Point and Liverpool works were unregulated by the State. Salt boilers in these areas were considered squatters and could be prosecuted; however, the law was not enforced.[10]
Salt Point to Salina
In 1794, James Geddes settled in Geddes on the west shore of Onondaga Lake and by 1796 he erected the first salt manufactory there. The Indians claimed the salt springs west of the lake, but they adopted Geddes into their tribe and allowed him to continue to produce salt. Other settlers came and over time, small clusters of log houses were built around the "scattered" salt works along the lake shore.[12]
Geddes was hired by the State in 1797 to survey Onondaga Salt Springs Reservation and lay out the first road in Salt Point.[12] During 1798, Salt Point became the village of Salina. The Surveyor-General, Simeon DeWitt, employed Geddes to design the streets. Although Geddes had no formal training in surveying, DeWitt saw great potential in him. Soon Geddes sold his interest in the Geddes salt works to pursue other interests and surveying continued to be an important role for much of his life.[12]
In 1804, an act was passed that directed the sale of 250 acres (1,000,000 m2) of the Onondaga Salt Springs Reservation for the purpose of "laying out and improving a road" running from lot 49, Manlius, to lot 38, Onondaga, east and west through the reservation. James Geddes laid out the design of the new road in "rather an irregular form so that as much dry land might be secured as possible."[17] The land, now the central portion of the city of Syracuse, was purchased by Abraham Walton for $6,650 and soon referred to as the Walton Tract.[12]
Boiling of salt
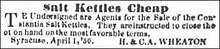
The Onondaga Indians of the mid-18th century, as well as European traders, produced salt by the boiling process.[4] Boiled salt was referred to as fine salt. From the earliest days, boiling was the preferred method of production because it was fast and could be carried out all year long in all kinds of weather. It was also very easy and economical for an individual or small enterprise to get started because it didn't take much room or equipment. In the beginning, the salt miners were either squatters or homesteaders, many were just passing through. They boiled salt as a pastime and used the finished product to barter for other goods.[2]
Most of the production methods employed were very basic. A kettle was hung on a branch which was suspended from two poles over a fire and the water gradually boiled away. Wet salt remained when the water evaporated and was emptied from the kettles and left to dry. Wood was plentiful and was used to maintain the fires.[10]
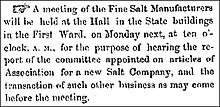
By 1791, approximately 8,000 US bushels (280,000 l; 64,000 US dry gal; 62,000 imp gal) of salt per year were produced on the reservation. Each bushel weighed 56-pound (25 kg). An early salt boiler usually produced 600 bushels a year, worth approximately one dollar per bushel.[4]
Boiling blocks
Increasingly, the salt manufactories were larger, commercial enterprises and the total amount of salt produced grew significantly. As the salt operations became more sophisticated, boiling blocks also known as salt blocks were constructed that consisted of large iron kettles "set into stonework and arranged in a double row" the entire length of a large shed-style building constructed for the purpose.[2] A boiling block was an area where men worked in 90 °F heat and high humidity, twelve hours a day, seven days a week, from April until November, boiling brine to obtain salt.[13]
The word block was derived from the masonry setting of the kettles. The kettles were hemispherical in form, cast-iron in material, and about 3 feet (0.91 m) in diameter. They were sunk in walls of brick or gray limestone from 50 to 100 in a row, sheltered in long, narrow houses. The walls were hollow, admitting the circulation of the fire of a furnace and the heat was driven under the kettles by a powerful blower. A worker tending the furnace would open the close fitting doors and shovel coal which "would disappear in the ferocious glow of the fire."[8]
The large kettles held 150 gallons and were placed nearest to the firing pit. A long flue ran the entire length of the shed and emptied into a tall chimney at the far end of the building. Smaller kettles, approximately 100 gallons, were placed further away from the fire, closer to the chimney where the heat was less intense.[2]
The pans would "bubble" with milky liquid and the vapor in the air was so dense that according to a local newspaper, the men working next to the kettles appeared "phantom-like hovering in a gauzy perspective."[8]
The boiling blocks contained as many as 80 kettles and operated 24 hours a day. The salt block owners at first burned hundreds of cords of wood per day but as the supply dwindled, 11 to 12 tons of coal per day were needed to sustain the fire. Each kettle would "boil down" every eight hours, or three times every 24 hours. Iron oxides and calcium chloride that settled in the bottom of the kettle were removed. Salt crystals were skimmed off the top with a long handled scoop and the remaining wet salt was placed into splint ash baskets to drain. A boiling block could produce three to four bushels in five hours.[2]

Each kettle held about 50 gallons of water, which was admitted from the cistern that contained calcium chloride, magnesium and gypsum (sulphate of lime) with a faint trace of peroxide of iron. When the water was boiled, these substances fell to the bottom where they were caught in a simple device known as a bittern pan which is a shallow basin of sheet-iron with an upright handle that projects above the surface of the water. All refuse created from the manufacture of salt was called bittern (magnesium chloride) and was extracted from the water in the form of chalky paste, which was discharged into a waste drain at either side of the kettles. A long pipe for conveying the water, passed between the two rows of kettles, each kettle drawing new supplies of water.[8]
In some cases, the kettles were heated inside steam jackets. The advantage was that all had the same steam pressure and the temperature was uniform. As a result, only one quality of salt was produced.[7]
Salt is also made by the "pan process" using direct evaporation over fire. Large wrought-iron pans that were 24 feet (7.3 m) wide, 100 feet (30 m) long, and 12 inches (30 cm) deep were used. The pans were divided into two sections by a loose partition, which allowed the brine to flow slowly from the rear to the front section. A second, smaller pan was set behind and slightly above the first, so that its contents could be siphoned into the front pan. Both were heated by flues from grates before the gases passed into the chimney. The pans were inclined and sloping wooden platforms, called drips, were joined to them on which the salt was drained. The brine was purified with milk of lime, the same as in the kettle process.[7]
The plant was in continuous operation, night and day, for about 14 days with two "runs" being made each month.[7] The State mandated that salt should be stored for 14 days in order to cure properly. The salt was packed into barrels for shipment which were tested by the State Inspector to make sure the salt was pure and properly dried.[2]
By 1872, there were 316 fine salt blocks and four large mills where table salt and dairy salt were produced. The vats and blocks were valued at $4.7 million. At that time, the industry employed 5,000 men and paid an annual tax of over $86,000 to the State of New York. An additional $80,000 was paid for canal tolls and $350,000 for freight on lake, river and canal.[11]
During the first year of regulated salt production in 1797, almost 26,000 US bushels (920,000 l; 210,000 US dry gal; 200,000 imp gal) of salt were produced and by 1872, that number had risen to nearly nine million bushels of salt.[11]
Erie canal
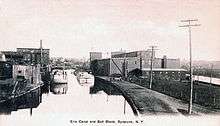
From the earliest days of the salt industry, the Central New York natural waterways including rivers and lakes, served as principal means of transportation. But these water routes were uncertain, difficult, and limited, and portages were slow and expensive. Syracuse salt manufacturers, especially Joshua Forman and James Geddes, were early "propagandists" on behalf of the Erie Canal project.[12]
The opening of the Erie Canal in 1825 caused a steep increase in the sale of salt, not only because of the improved and lower cost of transportation, but additionally, the ease of canal shipment caused New York State farms to change from wheat to pork production and curing pork required a lot of salt.[2]
After the War of 1812, it became difficult to obtain salt from abroad and commercial salt production became an important Syracuse industry. The Erie Canal allowed the bulky and low-priced Onondaga salt to be transported to Chicago and beyond via the Great Lakes relatively quickly and inexpensively.[18]
By 1837, the salt manufacturers, who were the main beneficiaries of the Erie Canal organized and suggested that the tax on a bushel of salt should be increased from .04 cents a bushel to .05 cents per bushel, which enabled eight million dollars of canal debt to be "liquidated." In 1838, taxes were raised to .06 cents per bushel, however, in 1846 they were reduced to .01 cent per bushel which was "ample" to cover the expenses of the State in connection with the Onondaga Salt Springs Reservation.[8]
With the lower freight rates on the canal, the production of salt increased rapidly, reaching a high point of eight million bushels annually during the Civil War period. Syracuse and Salina, situated on the canal halfway between Albany and Buffalo, and at the junction with the Oswego Canal, which opened in 1838, became important canal ports.[12]
By 1893, the salt industry was in decline and no longer a viable source of tax revenue for the State of New York, however, the Onondaga Salt Springs Reservation contributed over two million dollars toward the construction of the Erie Canal and Barge Canal.[9]
Although the Erie Canal was known by many names, those in Syracuse called it "the ditch that salt built."[18]
Salt potatoes
Salt potatoes originated in Syracuse and once comprised the bulk of a salt worker's daily diet. During the 19th century, Irish salt miners would bring a bag of small, unpeeled, substandard potatoes to work each day. Come lunch time, they boiled the potatoes in the "free-flowing" salt brine.[19]
By the early 20th century, the potatoes were a Central New York favorite and local entrepreneur, John Hinerwadel, started serving them as a side "at his famous clambakes." He later began packaging 5 pounds (2.3 kg) bags of potatoes along with a 12-ounce box of salt and labeled them "Hinerwadel's Famous Original Salt Potatoes." The brand is still available in the market today.[19]
Civil war
During the Civil War, salt production in Syracuse "secured the North's salt supply."[18] At the same time, Northern forces were in control of salt mines in Virginia and Pennsylvania, which meant southerners could not buy salt at any price. The salt shortage is believed to be one of the reasons the South lost the war.[18] Salt produced on the reservation was considered so critical during the Civil War that the salt workers were exempted from both jury duty[9] and military conscription in the mid-1860s.[13]
Solar evaporation
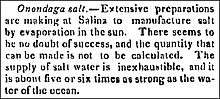
By the 1820s, the local supply of wood had been exhausted and the cost of importing coal from Pennsylvania was adding exorbitant costs to the production of Onondaga salt. Many salt producers began to switch operation from boiling their salt to the solar evaporation method by the mid-19th century.[2]
The idea of solar salt production was first conceived in 1821 by Judge Joshua Forman, who then resided in Syracuse and is considered the founder of the city. Together, with Isaiah Townsend, of Albany, New York, he traveled to New Bedford, Massachusetts, for the purpose of examining salt works that had been erected there. Forman met there with Stephen Smith, "with whom he counseled upon the subject."[20]
After Forman discussed the strength of the water in Onondaga Lake and its purity and abundance, Smith consented to "embark in the enterprise of erecting similar works" in Syracuse. Smith, together with William Rotch, Jr., Samuel Rodman and James Arnold of New Bedford, formed the Onondaga Salt Company. Smith was the controlling agent and Henry Gifford was superintendent of the construction.[20]
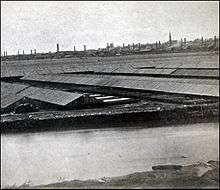
Forman traveled to Albany subsequent to the formation of the company and "procured the passage of a law by the Legislature, authorizing the company to take possession of the grounds and erect the necessary works." He later "applied" to Henry Eckford, a "celebrated" naval architect of New York, who consented, and with other local businessmen, established The Syracuse Salt Company. Eckford was then owner of the Walton Tract, which encompassed a large section of downtown Syracuse. Forman was appointed as agent of the company and Matthew L. Davis, secretary.[20]
During that period, the Salt Springs were called the Old Federal Springs. The water was pumped by hand labor by men "perched on high stagings, and collected into rude reservoirs for distribution."[20]
The two companies were formed and immediately set about the execution of their plans. The first thing done was to cut away the trees and clear the grounds in the area between the "Genesee turnpike" and the Erie Canal. This was an "almost impassable swamp" but clearing the land was preparatory to the erection of the first salt vats. The two companies, at their joint expense, erected the "first great reservoir, pumps and aqueducts at Salina" for the purpose of securing a greater supply of water. The machinery was propelled by surplus water from a branch of the canal and the "starting point" for the vats was just north of Church Street.[20]
After the two works were "fairly under way," the Onondaga Salt Company broke ground west of Onondaga Creek, near the dwelling subsequently occupied by Joseph Savage, where "the first growth of trees was still standing" and yielded 100 cords of wood per 1 acre (4,000 m2) .[20]
The building of vats "was prosecuted with great diligence and energy" and approximately 2,000,000 feet (610,000 m) of lumber was consumed annually for a period of several years in order to construct the vats.[20]
By 1826, Gifford's salt works covered 20 acres (81,000 m2) on ground on "private account;" however, he was unable to procure water for three years.[20]
For the first 44 years of salt production, only boiled salt was manufactured; however, by 1841, a grand total of 220,247 barrels of solar salt was produced annually. This number steadily increased for the next 40 years.[21]
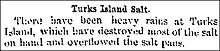
That same year, the Legislature ruled that all salt manufacturers could lease their land for 30 years in an attempt to reduce the number of lawsuits that had resulted by "virtue of the question of priority of leases."[9]
The production of salt by solar evaporation, also known as solar salt, required brine of a higher concentration than was available from the local salt springs. Shallow wells were constructed in an attempt to find more concentrated brine. Solar evaporation was also a slower method and wet weather, which was common in the area, could delay the process, however, it did prove to be cost effective and by 1864, solar reduction had become the primary means of salt production. Large areas of the lake shore were set aside for salt fields. One disadvantage was that solar salt could only be produced during the warmer months between April and early November.[2]
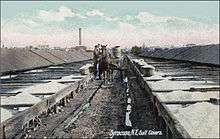
The solar method was performed in three phases ;[2]
- Brine was pumped through log pipes into vats in deep rooms[7] where the iron oxides and "casox" settled to the bottom. The tanks in these rooms averaged 18 feet (5.5 m) by 16 feet (4.9 m) by 8 inches (20 cm) through 12 inches (30 cm) deep and were from 200 feet (61 m) to 2,000 feet (610 m) in length, depending on the size of the yard. The vats were made out of pine plank. This process took two weeks.[8]
- The brine then passed to the salt rooms also known as lime rooms,[7] through a series of shallow vats 10 inches (25 cm) deep where gypsum (sulphate of lime) settled to the bottom and the brine was reduced through further evaporation. This process took seven days. During this period the local newspaper noted that the salt "shimmered and glowed" under the sun, and the vats looked like "hundreds of mirrors."[8]
- The concentrated brine was then transferred into shallow wooden trays that were 3 inches (7.6 cm) deep, commonly referred to as covers because they had a movable roof-like structure that was used to cover the brine during rain and at night. The roof was low and steep and moved on wheels over a steel track. Witnesses noted that the "motion of the covers seen from a distance seemed to make the earth ripple."[8]A loud bell was rung at the first sign of inclement weather and men, women and children "rushed out of shanties into the salt yards to push the covers over the vats."[8] Some of the salt yards contained as many as 15,000 covers. The brine was left open and exposed and by the end of the seventh day, crystals of coarse salt appeared on the surface of the vats, sometimes as thick as .5 inches (1.3 cm). The salt was allowed to accumulate until it was half the depth of the vat.[7]Solar salt workers in Syracuse, New York, about 1900
Once salt crystals formed, they were broken apart and pushed to the edge of the cover and the crystallized salt was transferred to carts for transport to the State storage warehouses where it was raked together and placed into tubs with perforated bottoms drained for 14 days before being packed in barrels for the market.[8] The salt was "harvested" approximately three times a season.[7]
A local news reporter in 1878 noted that the "gray that from a distance had seemed to overspread the ground was not mist, but acres and acres of box-like vats, in which the brine was evaporating." The vats and roofs were made of unpainted timber, which the weather had stained gray. "There was nothing to indicate that thousands of men were employed on the ground in the salt business, an impressive air of quietude and inaction possessing this scene."[8]
By 1900, there were over 43,000 salt covers with an evaporating surface of over 12,000,000 square feet (1,100,000 m2). During a good season, from three to four million bushels of salt were produced.[2]
All operations on the salt fields were suspended during the colder months, from early December until March 1 each year. Hence, the average "working" year was only 70 days long, as there was only a short timeframe the weather was warm and dry enough for salt to evaporate by the solar process.[8]
Salt wells
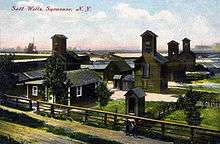
The first salt brine used in early production came from the naturally occurring springs and shallow wells dug into swampy land on the lake shore. In 1806, the first "deep well" was sunk and was recorded at a depth of 30 feet (9.1 m). The brine was pumped to the surface with hand pumps, which could produce about 40 gallons per minute.[2]
Beginning in 1838, the State authorized the drilling of deep wells at several locations around the lake to locate the source of the brine; however, none of the wells that were drilled were able to pinpoint the source.[2]
By 1878, the wells were 300 feet (91 m) to 450 feet (140 m) deep. When the "cemented earth" was pierced by a drill, the salt-water rose to within 18 feet (5.5 m) of the surface and was raised the remainder of the way by small pumps driven by steam. That year, it was estimated that a total of over 200 wells had been sunk since 1797, at a cost of $750,000 and a yield of salt that was nearly 300 million bushels, or enough to cover a surface of 120,000,000 square feet (11,000,000 m2) with solid salt 12 inches (30 cm) deep. In 1878, 38 wells were in use and seven million bushels were produced annually.[8]
The wells were enclosed in well "houses" that had "dwarfed towers." They were not simple excavations, like garden-wells and instead, were narrow and deep. The brine was obtained by boring wells 8 inches (20 cm) to 10 inches (25 cm) in diameter which were lined with iron casings to eliminate contamination from surface water.[7] The iron casings were driven in lengths of 18 feet (5.5 m) to the depths of the brine. When the length was driven, another would be screwed to it, and that would be forced down by pressure from above. Length after length was added, until a continuous pipe of 300 feet (91 m) or 400 feet (120 m) was formed and the salt water "bubbled up."[8]
Salt Wells at Syracuse, New York about 1900This is a description of the landscape around the lake made by a news reporter approaching on a train in 1878;
" Partly within and partly outside the limits of Syracuse. that charming little city in the center of New York State, the landscape, which is walled in by low hills, receives a peculiar character from the presence of gloomy clusters of buildings, nearly uniform in size and quite different in shape from any others in the neighborhood. They are gray and weather-beaten, and on overcast days, they look as oddly fantastic as the windmills of the Netherlands. Square brick chimneys tower among them, and pour out wavy clouds of black smoke and white steam. Just behind them is a lake, the further bank of which shows slanting meadows. The buildings are oblong, and the roofs are steep and topped at one end by thick towers, which are monstrously out of proportion to the rest of the structure, reminding us of ambitious church steeples with their tops cut off. A view from an elevation shows that there are four separate groups or clusters and that they are built on low ground, which apparently, from some undiscoverable cause is overspread with gray.
'What are they?' is a question often asked by passengers on the trains from which they are visible, but unless the inquiree speaks within the hearing of a resident of the city, it is probable that the closest approximation to truth is the answer volunteered, will be a statement that they are the Onondaga Salt Mines, the fact being that they are wells."[8]
Salt pumps
“ | The reservoir, like all the other buildings, is very much weather stained. The inside of the pumping house is always moist and reverberant and the machinery is always in a cold perspiration. The laborers toiled inside the pump house on precarious looking scaffolding. The muscles of the common laborer with ten hours of physical toll a day for exercise do not attain the iron quality of those of the amateur athlete, exercise without good food and careful training is only a wasting process, a fact impressed upon us by the spare frames of some of the men about the salt works. News reporter in 1878.[8] | ” |
The State operated water and steam powered pump rooms in each of the four districts; Geddes, Liverpool, Salina and Syracuse. The pumps forced brine water from the lake into tall reservoirs.[13]
The brine was raised by pumps with an endless wire rope chain that was powered by an engine. When the brine reached the surface, it had a slightly "turbid appearance." This was the result of the brine mixing with clay and fine sand raised from the well, together with small bubbles of carbon dioxide. The brine also contained ferrous carbonate which was held in the solution by carbon dioxide. As the carbon dioxide escaped, the ferrous salt absorbed oxygen from the air and the hydrated ferric oxide separated as a "yellowish red turbidity," which settled after a short period, leaving behind a clear brine.[7]
Brine was pumped from the salt wells into small settling tanks and from there it was channeled through wooden log pipes to a central distribution tank which was set at an elevation higher than the boiling blocks so that flow could be controlled by gravity. If the central storage tank was lower than some of the boiling blocks or solar fields, the brine would have to be pumped into a large reservoir located at the top of an 80 feet (24 m) tower-like structure situated on adjacent high ground. From this tower the brine was conducted through wooden pipes by its own gravity to the various manufactories on the reservation.[8]
The pump was driven by an overshot water wheel which was 22 feet (6.7 m) in diameter. A back-up steam pump was close by in case of break-down. The pump operated from the beginning of April to late November or early December, depending on weather conditions as the wheel could not operate once the canal froze. Boiled salt could be produced each year only as long as the water wheel turned.[2]
In the 1890s, a new system was developed for pumping the brine from deep wells using compressed air. This method produced about 150-160 gallons of brine per minute from wells that were 100 feet (30 m) deep.[2]
Log pipes
Wood marketing flourished in the city and the forest was cleared to supply fuel for local salt boiling, lumber for new homes and boat building. The pepperidge (Nyssa sylvatica) (also known as tupelo) tree was particularly adapted for "brine-pipe" use in the salt industry were so valuable and in such high demand, the tree is now virtually extinct within a radius of 10 miles (16 km) of the city.[22]
The pipes were examined in 1940 by Harry P. Brown, professor of wood technology at the State College of Forestry in Syracuse who determined that the brine pipes were constructed from both Nyssa sylvatica or Nyssa aquatica, also known as tupelo and grown in the south. He "regarded it as interesting" that so much wood was available in the area, most of which was from the native northern tree, "for it is of scattered growth, its seed spread by birds."[22]
The pipes were made from logs, commonly known as elm logs, which were hollowed out and the end was inserted into another log pipe and bound by "iron ribbons." There were 50 miles of pipes that could be seen all over the reservation which "look like gray snakes as they follow the undulations of the ground, creeping up the walls of buildings and bridges of trestle work." The pipes were always laid above ground and were "said to be very durable."[8]
Packaging
“ | The table salt was exquisitely fine in grain and immaculately white. White strikes the eye of the visitor everywhere in the building, in pyramids 12 or 15 feet high, in little drifts, all over the floor, on the workman's clothing and in a dust that settles like a silvery mist.[8] | ” |
Both solar salt and block salt were coarse-grained when they left the reservation. The solar salt was put to use in preserving pork and "such base purposes" and a large proportion of the block salt was refined for table salt.[8]
The power from the main engine was carried to other parts of the building by wheels, shafts and leather bands. In one room, the finished product was washed, for "despite the attention it has received" in the boiling houses, some of the chlorides of calcium, magnesium and gypsum remained behind. The salt was placed into a shallow tube partly filled with water, where it was turned over and over and up and down by corkscrew-like shafts until every particle of alloy was separated. The refuse was sold by the refiners to farmers for agricultural purposes at $1.50 a ton.[8]
After the salt had been washed it was dried in long, iron tubular cylinders, which revolved over furnaces in a constant motion until the salt was as parched and as hot as desert sand, the vapor parsing from it through steam vents. It was next carried upstairs by an endless chain of small buckets. The buckets loaded and unloaded themselves automatically. On the upper floors, the grinding was done. Salt intended for dairy purposes was ground between granite rollers and that intended for table use was put through an ordinary flouring mill.[8]
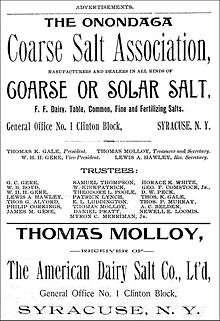
A number of young women dressed in "showy prints" and with their hair tied up in "variegated kerchiefs," scooped the salt up into small cotton bags and sewed them up with "astonishing speed." The bags were then packed in barrels and shipped to market.[8]
An analysis of the quality of the salt in 1876 made by the Butter and Cheese Exchange reported that the Syracuse dairy salt was "superior to all others" and had a lower level of total impurities. There had been a long-standing prejudice by dairymen against Onondaga salt because of perceived impurities which were proven false.[15]
Salt producers
In 1850, the singer Jenny Lind made a professional visit to Syracuse, appearing in a concert at the National Theater. She ended up staying an extra day in order to visit the salt fields. An enterprising marketer was quick to appreciate the advertising possibilities of the visit and historical records show that a short time later, the Jenny Lind brand of salt was placed on the market.[23]
In 1860, the local manufacturers united and formed the Salt Company of Onondaga. The property was valued at $3,200,000.[9]
During 1874, Ashton Salt Mill was operating in the town of Geddes, on the western edge of the city and Saginaw Salt Works was located southwest of the city in the town of Onondaga. That same year, several other salt producers were operating within the city limits including; G. A. Porter & Company, Haskin's Salt Mill and J. W. Barker & Company.[24]
In 1878, Geddes was the home of Western Coarse Salt Company, Turk's Island Coarse Salt Company, Geddes Coarse Salt Company, Union Coarse Salt Company, Cape Cod Coarse Salt Company, W. & D. Kirkpatrick of No. 7 Wieting Block, Draper & Porter, W. B. Boyd, Mrs. S. O. Ely and J. F. Paige.[25]
During 1879, the city directory had a list of salt manufacturers Excelsior Dairy Salt Company located at 1 Syracuse Savings Bank Building, McChesney & Caten at 81 East Water, N. Y. S. Salt Springs at 58 North Salina, Salt Springs Solar Coarse Salt Company of 6 Wieting Block and Star Salt Mills at 8 North West. There were also individuals listed such as Robert Young of Green Point Road, Samuel H. Burritt and George A. Porter, both of Basin near Court Street.[26]
In 1893, The American Dairy Salt Company, Ltd. had their general office at No. 1 Clinton Block in Clinton Square.[5] The Onondaga Coarse Salt Association were manufacturers of coarse or solar salt including; dairy, table, common, fine and fertilizing salts. By 1884, Thomas Gale was the president, J. W. Barker was secretary and Thomas Malloy was treasurer.[5] In 1893, Thomas K. Gale was still president, Thomas Malloy was the receiver and treasurer, W. H. H. Gere was vice-president, and Lewis A. Hawley was recording secretary.[27] In 1910, the company was shipping salt to Canada.[28]
Revenue and expenses
Revenue derived from the manufacture of salt was paid to the New York State Treasury and credited to the general fund.[9]
In 1874 the total amount of salt produced was 6,029,300 bushels and duty paid was $60,293. By 1875, the number rose to 7,179,446 bushels and duty paid was $71,794. During that same period, the expenses amounted to $65,972 which meant total revenue was $66,115.[15]
Solvay process
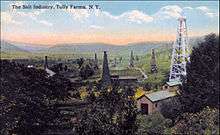
In 1888, the Solvay Process Company established a chemical plant along the southern shore of Onondaga Lake to manufacture soda ash from the halite and limestone found within the bedrock. The concentration from the springs and wells in the Onondaga Salt Springs Reservation gradually diminished over the years and this forced the company to seek additional sources of brine.[4]
Salt wells that tapped into halite (common salt) beds in the local Salina shale near Tully, New York, 15 miles south of the city were developed in the 19th century. The north flowing brine from Tully was the source of salt for the "salty springs" found along the shoreline of Onondaga Lake.[4]
The company drilled several deep test holes in the area south of Syracuse and eventually encountered halite deposits at a depth of 1,216 feet (371 m) below land surface in the southern end of Tully valley. More than 120 wells were drilled into four halite beds on the east and west flanks of the southern part of the valley from 1890 through 1986. The brine withdrawn from the Tully valley brinefield over a 96-year period resulted in the extraction of more than 96 million tons of salt.[4]
Lake water level
The outlet of Onondaga Lake was lowered in 1822 for construction of the Erie Canal which permanently lowered the water table around the lake.[4]
By 1882, the lake's water level was lowered after the outlet to the Seneca River was dredged. As a result, the low lying swampy area the northern end of downtown Syracuse was drained and filled. The wetlands were eliminated, which had the positive effect of greatly reducing the threat of malaria for residents of the growing city.[29]
The water level in Onondaga Lake was again raised when the Barge Canal was completed in 1918.[29]
Salt water for cooling
From the mid-19th century through the early 20th century, many companies that did not produce salt were also established in the Onondaga Creek Valley. Several of these businesses dug or drilled wells into the underlying sand and gravel aquifers to obtain water for cooling purposes for use in production of goods such as beer and dairy products as well as storage of perishable goods. The wells were also used to regulate temperatures in office and storage buildings.[2]
The water obtained from these wells had a nearly constant temperature of 50–52 °F and ranged in chemical character from saline to brine. The water later was discharged and drained back into Onondaga Lake. Although this process did not utilize the salt resource, it took saline water from the ground-water system and released it into freshwater streams. Ultimately, this increased the salinity of the surface-water system.[30]
The use of ground water for cooling purposes in the area declined and eventually ceased with the advent of air conditioning. It is currently unknown the total amount of salt withdrawn from the aquifer system, nor the exact number of wells or their locations. The presence of these wells is of concern because the old and decaying well casings could "provide a hydraulic connection between the brine-bearing sand and gravel aquifers and the surface-water system."[4]
Western competition
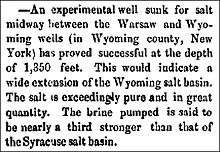
After the Civil War, the salt industry began to decline. By 1876, there was increased competition with the strongest rivals in Michigan and Canada. Every effort possible was made to improve the brine in order to put Onondaga salt in a position to "cope" with its new rivals and increase the revenue of the state.[15]
Throughout the early 1870s, the State had taken several steps such as sinking new deep wells in order to increase the average salinity of brine taken from the reservation, thereby decreasing the amount paid for the coal used to reduce it to salt and make it more competitive in the market.[15]
The State also experimented with several methods to more efficiently remove escaping steam from the boiling brine without any satisfactory results. Chemists spent seven years and over $100,000 in an attempt to use "superheated" steam passed through steam-pipes as well as heated air applied in various ways to assist the evaporation in the kettles and to save fuel. Patent furnaces and grates were also tried without sufficient results to pay for the extra expense.[15]
The Godrich steam pan was built at great expense but abandoned as a failure. Two of the devices did produce good results including the Godrich plan with "hanging tubes" and the Gilson cylinders, although fuel saving was not realized which made "general adoption" out of the question.[15]
In November 1882, an experimental well was sunk in Wyoming County, New York, at a depth of 1,350 feet (410 m). This revealed a "wide extension" of the Wyoming salt basin. The salt was "exceedingly pure and in great quantity." The brine pumped was nearly 33 percent stronger than that of the Syracuse salt basin.[31] Both localities were part of the Onondaga-Formation.[4] The Wyoming deposits were south of Rochester and in the neighborhood of Warsaw and Batavia in Western New York.[7]
During March 1885, a vein of salt was discovered near Phelps while an oil company was boring for petroleum near the town 20 feet (6.1 m) thick. According to a newsarticle; "The news of the discovery went like wildfire through the section and property owners were elated."[32] Soon after, a company of wealthy citizens in Phelps and Clifton Springs was formed to manage the mines. Pumps were immediately set up and a large manufactory was constructed during the summer of 1885.[32]
Additionally, many new salt reserves were discovered out west in Wyoming and Utah.[13]
End of production
By 1900, in addition to competition from salt producers out west, the ever increasing costs for both the manufacture and transport of the finished product, plus the discovery that the salt salinity in Onondaga Lake was weakening, contributed to the end of the salt industry in Syracuse.[13]
During 1908, the State of New York auctioned off its pipelines, pumping machinery and reservoirs to private industry. The Salt Springs Superintendent, who reported to the New York State Legislature, was let go in 1914. After salt production was discontinued by the State, it fell into the hands of private industry, although some of the land was still owned by the government.[2]

The demise of the salt industry, despite its importance for so many decades, surprisingly was hardly noticed by residents of the city. The economy was booming and several features including the central location of Syracuse combined with its railroads and canals, access to raw materials and the presence of gypsum, brine, and limestone, and a large labor supply, all combined to attract varied industries. Eventually, the acreage devoted to salt works became more valuable as factory sites and the old industry was "forced out."[12]
By 1920, the majority of salt produced was used to pack fish and in ceramic production at local companies such as Syracuse China. Salt was also used to de-ice the local railroad and trolley tracks during the winter months. Additionally, the salt brine was in demand by the chemical companies such as Solvay Process Company that were gradually replacing the salt manufacturers along the shores of Onondaga Lake.[2]
In 1922, a wind storm left much of the remaining salt yards in ruin. Some repairs were made and the industry struggled along until August 1926, when the last nine salt workers drew the final batch of brine and the salt industry closed its doors.[2] The Onondaga Coarse Salt Company, the last manufacturer, had been in business for 125 years.[13]
With the discovery of large deposits of natural sodium carbonate Trona in 1938, near Green River in Wyoming, the Solvay process became uneconomical and the Solvay Process Company plant closed permanently in 1985. There are no Solvay plants in operation now in North America; however, throughout the rest of the world the process remains the major source of soda ash.[4]
The closing of the Onondaga Salt Springs Reservation in the early 20th century and the end to mining brine in the southern part of the Tully valley in the late 20th century marked the final chapter of salt mining in the Syracuse region, but groundwater flowing along the southeastern shore of Onondaga lake in Syracuse still allows salty water from a 1,000 feet (300 m) below the southern Tully valley to flow by gravity feeding salt springs around the lake where the Salina shale contains no halite beds.[4]
Salt city
The rapid development of this industry in the 18th and 19th centuries led to the nicknaming of Syracuse as "the Salt City."[4] From 1797 through 1917, the Onondaga Salt Springs Reservation produced more than 11.5 million tons of "finished" salt.[33] Additionally, the withdrawal of brine from the Tully valley brinefield area by Solvay Process Company over a 96-year period resulted in the removal of more than 96 million tons of salt.[4]
The days of salt production in Syracuse are long over, however, the city still honors the industry in names like Salina Street which is the main street through downtown, Solar Street, Salt Springs Road and the town of Salina, New York.[13] There is also a neighborhood enclave in Syracuse named Salt Springs.
Salt Museum and Parks
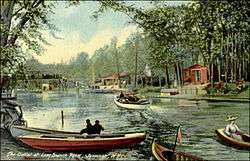
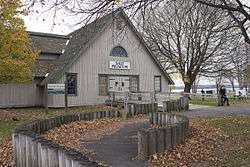
The abandoned Onondaga Salt Springs Reservation became a dumping ground in the early 20th century, however, the Great Depression brought new life to the area when Governor Franklin Delano Roosevelt turned the State land over to Onondaga County during the New Deal era. Funding from the Work relief program, and the organization of the Onondaga County Emergency Work Bureau helped the county convert the area into Long Branch Park during the early 1930s.[13]
Included in the project was the construction of the Salt Museum which was built around a "still standing" boiling block chimney. The building stands on the site of the Sampson Jaqueth Salt Manufactory which was erected in 1856. One-third of the original chimney survives.[13] The museum opened in 1933 and is still in operation.[2] The museum is operated by Onondaga County Parks Department and is closed during the winter months.[13]
News articles
![]() Caution - Onondaga Salt - It has lately been discovered that lime has been mixed with some of the salt - The Ohio Repository - April 26, 1821 |
![]() Onondaga Salt shortage. Rochester Telegraph, October 8, 1825 |
![]() Onondaga Salt - Quantity sold is less than last year. Syracuse Journal, November 19, 1856 |
References
- 1 2 Beck, Lewis C. An Account of Salt Springs in Salina, in Onondaga County, State of New York. J. Seymour printer, New York, 1826, p.36.
- 1 2 3 4 5 6 7 8 9 10 11 12 13 14 15 16 17 18 19 20 21 22 23 24 Bell, Valerie Jackson. "The Onondaga New York Salt Works (1654 - 1926)". Science Tribune, October 1998. Retrieved November 5, 2010.
- ↑ Salt production. Encyclopedia Americana, New York, 1968, vol.26.
- 1 2 3 4 5 6 7 8 9 10 11 12 13 14 15 16 17 18 19 Kappel, William M. "Salt Production in Syracuse, New York" (PDF). USGA, November 2000. Retrieved November 6, 2010.
- 1 2 3 Boyd's Syracuse City Directory 1884. Andrew Boyd, 1884.
- ↑ Mather, Frederic G. "The Salt-Deposits of Western New York". Popular Science Monthly Volume 25 - August, 1884.
- 1 2 3 4 5 6 7 8 9 10 11 "Salt". Lenntech Water treatment & purification Holding B.V., 1998. Retrieved November 19, 2010.
- 1 2 3 4 5 6 7 8 9 10 11 12 13 14 15 16 17 18 19 20 21 22 23 24 25 26 27 "Among the Salt Makers". The Syracuse Standard. Syracuse, New York. January 19, 1878.
- 1 2 3 4 5 6 7 8 9 10 11 12 13 "The Onondaga Salt Springs". The New York Times, June 10, 1893. June 10, 1893. Retrieved November 13, 2010.
- 1 2 3 4 5 6 7 8 9 10 11 12 "Early History of Syracuse". Shades of Oakwood, 2010. Retrieved November 5, 2010.
- 1 2 3 4 F. Rives, J. Rives & George A. Bailey. City of Washington: Office of the Congressional Globe. United States Congress, 1872. Retrieved September 9, 2010.
- 1 2 3 4 5 6 7 8 9 10 "New York, Syracuse". Atlantis, 2010. Retrieved November 3, 2010.
- 1 2 3 4 5 6 7 8 9 10 11 12 Chan, Sewell (December 31, 2009). "On the Road: A Proudly Salty Reputation". The New York Times, New York, New York, December 31, 2009. Retrieved November 8, 2010.
- 1 2 3 Joshua Victor Hopkins Clark. Onondaga, or, Reminiscences of earlier and later times, Volume 2. Stoddard and Babcock, Syracuse, NY, 1849. Retrieved September 6, 2010.
- 1 2 3 4 5 6 7 8 "The State Salt Springs". The New York Times. New York, New York. February 12, 1876.
- ↑ "Biographical Directory of the United States Congress". U.S. Congress. 2010. Retrieved December 6, 2010.
- ↑ Bannan, Theresa. Pioneer Irish of Onondaga: (about 1776-1847). The Knickerbocker Press, New York, 1913. Retrieved October 23, 2010.
- 1 2 3 4 "Salt Mines and Brine Wells in the Finger Lakes". ILovetheFingerLakes.com, 2010. Retrieved November 10, 2010.
- 1 2 "Syracuse Salt Potatoes". Just Good Eats, 2004. Retrieved November 9, 2010.
- 1 2 3 4 5 6 7 8 Timothy Collingwood Cheney and Parish Barkydt Johnson. "Early landmarks of Syracuse". Electronic Library, 2010, pg.12. Retrieved October 28, 2011.
- ↑ "Census Bulletin Tells of Onondaga Salt Industry". The Post-Standard. Syracuse, New York. December 10, 1901.
- 1 2 "Bicycle and Automobile Set New Tempo and Brought More Industry to Syracuse". The Post-Standard. Syracuse, New York. January 31, 1940.
- ↑ "Prosperous Syracuse of 1910 Teems With Industrial Activity". The Post-Standard. Syracuse, New York. September 12, 1910.
- ↑ "Partner Information U.S., Indexed County Land Ownership Maps, 1860-1918 Record". Ancestry.com, 2010. Retrieved 2010-08-30.
- ↑ "History of the Town of Geddes". D. Mason & Co., Syracuse, New York - 1878. Retrieved 2010-08-30.
- ↑ Boyd's Syracuse City Directory 1879. Andrew Boyd, 1879.
- ↑ Syracuse City Directory. Syracuse, New York. 1893.
- ↑ "Syracuse Industrial Products on Sale All Over the World". The Post-Standard. Syracuse, New York. September 12, 1910.
- 1 2 "History of Onondaga Lake". Onondaga Community College, 2010. Retrieved November 20, 2010.
- ↑ Higgins, Jr., G. L. Saline Ground Water at Syracuse, New York. Syracuse University Department of Geology, 1951, p.87.
- ↑ "Over the State". Bucks County Gazette, November 19, 1882.
- 1 2 "New Salt Mines". Frederick, Maryland - The Daily News, March 19, 1885.
- ↑ Phalen, W. C. Salt Resources of the United States. U.S. Geological Survey, Washington, D.C., Bulletin 669, p.275.
External links
![]() |
Wikimedia Commons has media related to Salt industry in Syracuse, New York. |
- Salt Production in Syracuse, New York- United States Geological Services, November 2000
- The Onondaga New York Salt Works (1654 - 1926) - Science Tribune: Bell, Valerie Jackson, October 1998
- History of Onondaga Lake - Onondaga Community College, 2010